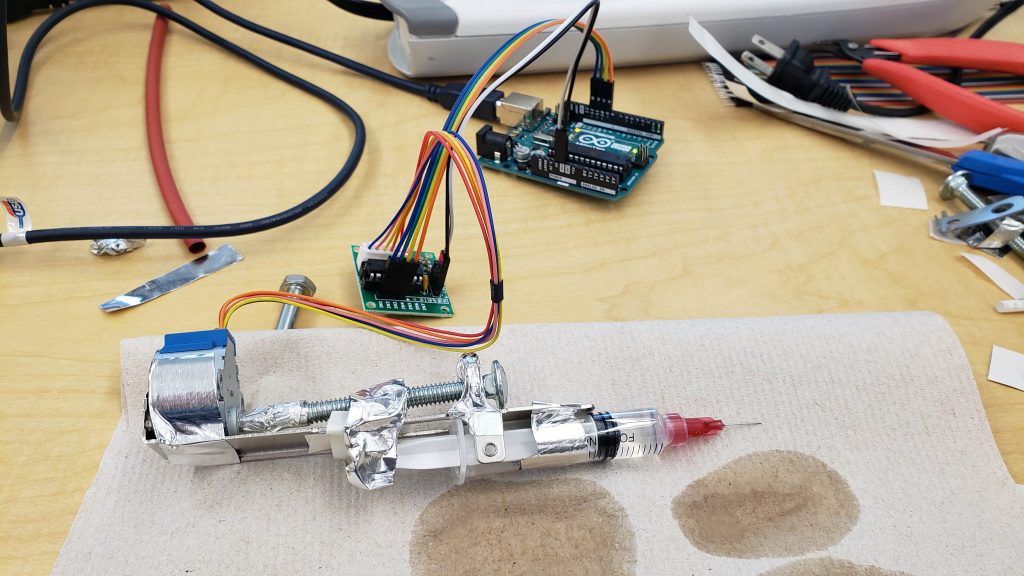
Or, three hours enjoyably lost to a visit from the bad idea fairy.
My PhD advisor and I were chatting in the lab today and had an idea that it would be interesting to try to drip/jet a bit of water onto just-extruded filament, ideally in small enough quantity that it phase changed and flashed off with all the excess energy, in order to allow printing unreasonable unsupported structures.
It unfortunately doesn’t look like it will be practical, but we got a PoC-grade implementation in a few hours and it seemed worth a quick write-up to document our experiment for the interwebz.
We’ve previously had success with added air cooling to get through tricky prints with thin sections and/or unsupported steep angles, and are both familiar enough with machine tools to think of flood and mist type cooling from that world, and they seemed like a likely combination. We also both had writing we didn’t want to be doing, and so we decided to try it right now since I had some dosing syringes in one of my parts drawers left over from some project or another.
First pass test was to see if I could hand-hold a syringe next to a printer head as it purged into the air and spray water on it. To test for efficacy, we poked the output with a pair of tweezers as it came out to see how much bend it could be coerced to take under various amounts of water being sprayed on it. Initial results were promising, normally filament purged into the air is a limp noodle, and we could set sub-5mm bends into it when the water was being applied. The best strategy seemed to be to apply just enough pressure to maintain a small water bead on the extruded plastic, rather than squirting a stream or dripping intermittently. It’s also remarkable how little water is needed to completely flood 0.4mm extrusion. I think all our experiments consumed maybe 8mL in total; pressing hard enough to make a continuous stream looks like ridiculous overkill at the print head. No pictures of this part because it required all available hands.
With that first level demonstration showing promise, I went parts bin digging, and between my on-hand parts and the lab’s on-hand parts, I hacked up the world’s jankiest syringe pump, strapped it to the lab’s least-loved printer, and had proof of concept in an hour or so. While I put that together, Hank designed some minimal-example coil-on-platform test prints and wrangled our long-neglected Wanhao i3 into working-enough order.
The parts assembled include:
- 1x 5mL syringe
- 1x 25GA applicator needle
- 1x ULN2003 Darlington driver on breakout
- 1x 28byj-48 Stepper motor
- 1x Arduino Uno
- Assorted jumper wires
- 1x long-ish 1/4-20 bolt
- 1x 1/4-20 wingnut
- 2-ishx 1/4″-ish washers
- 1x PCI Port Cover
- An alarming quantity of aluminum duct tape (including a bit of the backing to use as “bearings”)
It is the first time I’ve ever found an actually useful application for a 28byj-48, despite them being a parts bin staple – every other time I’ve grabbed one they’ve either been out-competed by a little servo or the feebleness and gearing required a step up to a more substantial stepper motor. Assembled in a less-wretched way, this thing would probably be a genuinely useful piece of lab-ware, and not cost $1500+ like the commercial versions. The Arduino code was an absolute minimal hack around around AccelStepper that let me set the step rate from a serial terminal.
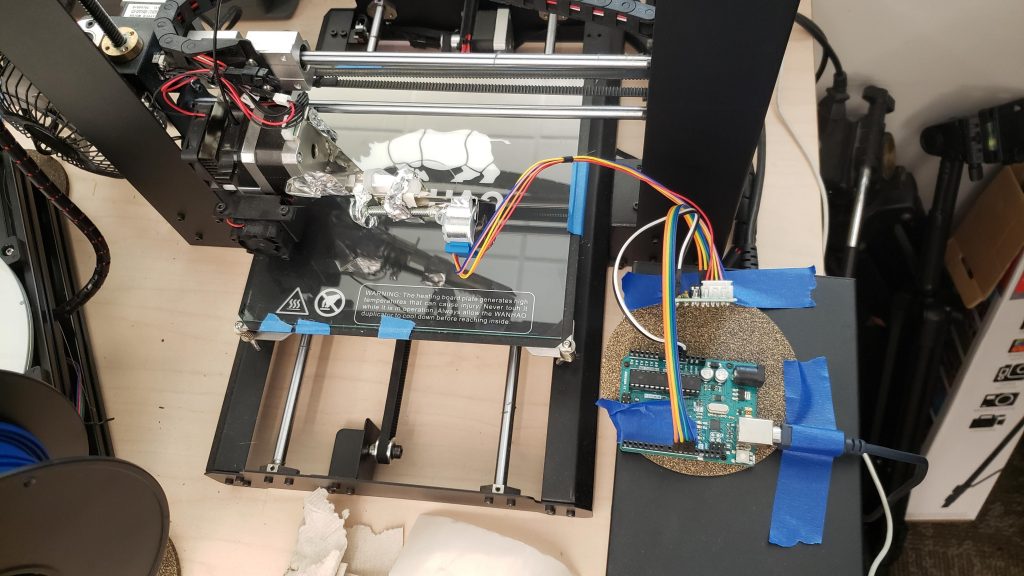
The resulting monstrosity was then taped to the extruder of the printer so the needle was slightly above the nozzle, pointed at the most recently extruded filament. The motor part was “delicately” cantilevered so that it didn’t whack into anything during the necessary range of motion.
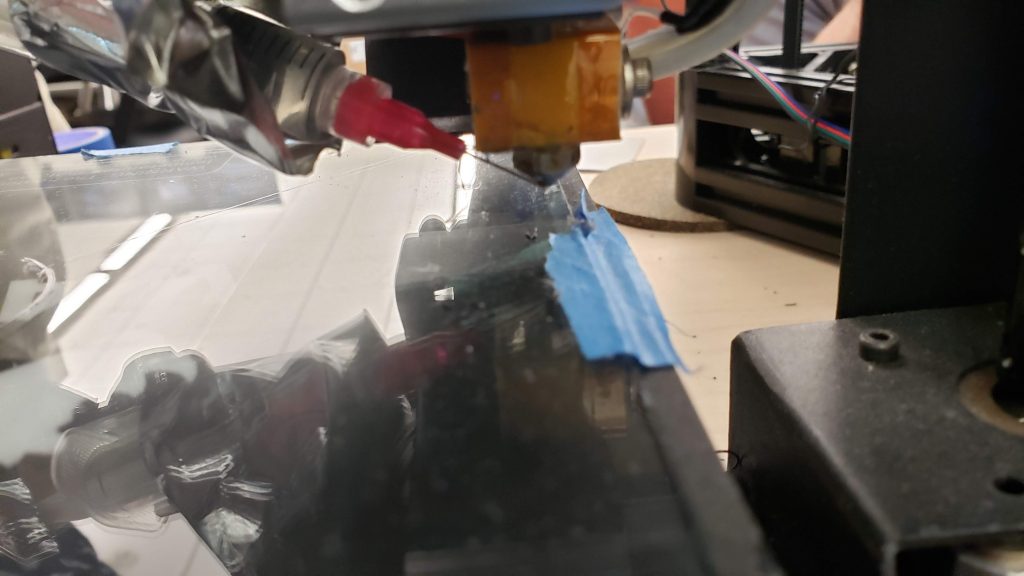
And now for the sad part, it doesn’t seem to work as desired. We could set the flow rate to generate a similar hanging water drop phenomena to what I got by hand during straight extrusion, but in actual printing the water seemed to inevitably wick back up on to the nozzle, boil, and crash the hot-end temperature rather than cooling the extruded filament. Maybe it would be possible to adjust so the relative positions just so such that the needle didn’t catch the already-printed part while the water stayed off the nozzle, but sticking with air-based solutions looks more promising.
At very least, it was an afternoon of research in which I actually learned something that another human being might care about, instead of the lately-usual “masturbating for imaginary prestige points” type research activity.
The experiment has also convinced me of the value of rigging up something similar to squirt small quantities of liquid coolant/lubricant out of a dispensing needle onto the cutter in my CNC router, maybe a system with a cheap peristaltic pump and some luer locks…. the beginning of the semester is probably not the ideal time for this discovery.